What to consider when comparing circulators
Performance does not equal efficiency
Good comparability of products is essential for users. For this purpose, DIN 12876 defines various characteristics and measurement methods that should be used as a basis for the characteristic data for heating and cooling thermostats. Characteristics recorded in this way enable a reliable comparison of performance.
If you compare the liquid temperature control devices available on the market, you will see that there are two concepts. In addition to the open bath thermostats, there are the closed temperature control systems, also called process thermostats. The latter class of equipment was first introduced over 25 years ago with the "Unistat Tango". The then completely new concept of the Unistat Tango brought a major technological advance in temperature control. In contrast to conventional bath and circulation thermostats, the "Unistat Tango" worked for the first time with a closed temperature control circuit. Unistats are, so to speak, circulators without a temperature control bath. An expansion vessel replaces the conventional bath for the thermally induced volume change, and the volume change takes place there. This principle reduces the masses to be tempered and thus increases the rates of temperature change. Due to these properties, Unistats are predestined for temperature control tasks in process engineering, such as reactors, autoclaves, miniplant/pilot plants, reaction blocks and calorimeters.
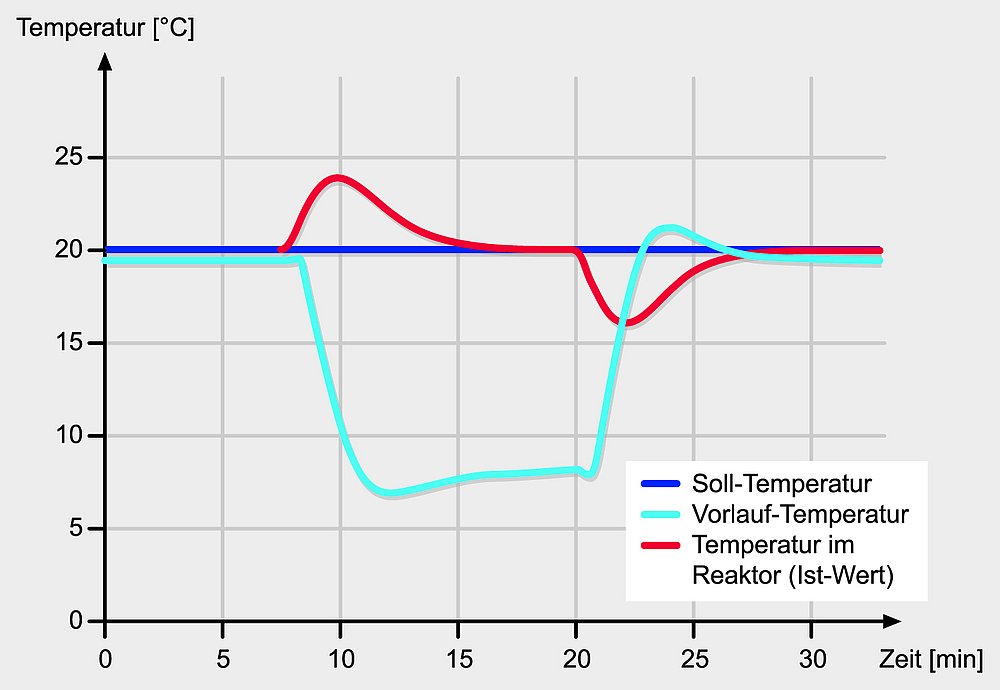
When asking about the dynamics of a temperature control unit, the heating or cooling capacity (kW) is usually used as a comparative variable. However, the power generated in the thermostat alone is not sufficient for a meaningful evaluation. An equally important aspect is the mass to be tempered. For a meaningful comparison, therefore, the cooling power density (Watt/liter) according to DIN 12876 is the most suitable. Basically, the greater the cooling power density, the more dynamically (quickly) a thermostat can respond to a temperature change requirement.
Let's assume we have two temperature control units from different suppliers. The cooling capacity of both units is the same, as is the flow rate (l/min) and both temperature control units are connected to identical applications (e.g. glass reactor). To be able to make a statement of the dynamics (cooling time), we use the following formula:
P = m * c *dT/dt (P = power ; m = total mass ; c = spec. heat capacity ; dT = temperature difference ; dt = cooling time).
Converted to cooling time dt: dt = m * c * dT/P
Here, for the same temperature control task and liquid, the expression c * dT/P is the same for both applications. For the mass, however, it is worth taking a closer look.
Let us imagine that temperature control unit 1 has a mass of 5 kg (filling volume, not the unit's own weight). Temperature control unit 2 has a mass of 10 kg. The mass of the external application is 5 kg. In the first case, the total mass is 10 kg (internal filling volume plus external application), in the second case, 15 kg must be cooled (or heated). The ratio is 2 : 3, or in other words: it takes only 2/3 of the time with temperature control unit 1. The time saving is therefore 33 %.
This example shows that the cooling capacity is certainly an important factor. However, this should then be related to the quantity of temperature control liquid used. The result is the cooling capacity density, which can then be compared in a meaningful way (see DIN). By the way: Temperature control unit 1 also saves 1/3 of the temperature control liquid and energy each!
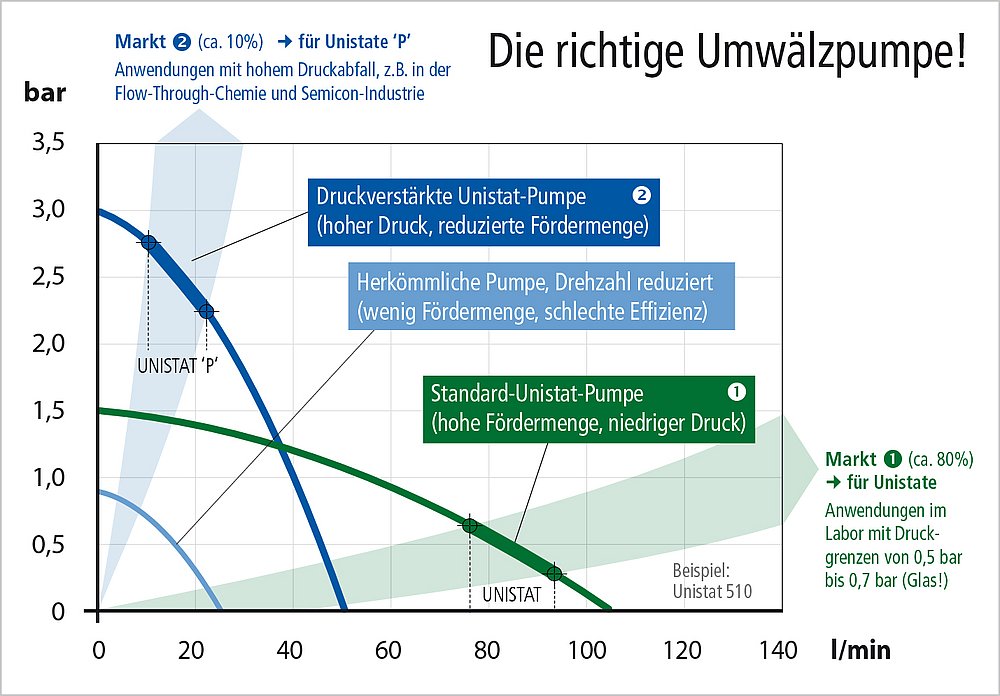
Another important criterion is the flow rate of the circulation pump. This has a strong influence on the heat flow that can be dissipated from the temperature control liquid by a refrigeration circulator. According to DIN, the cooling capacity must be measured at full pump capacity. At reduced pump capacity, the heat input by the pump motor is lower. This results in more net cooling capacity and allows lower temperatures. Important for most applications is not the pressure capacity (bar) but the highest possible flow rate (l/min). This is because temperature control is ultimately not about how much power a thermostat generates, but much more about the efficiency of heat transfer to the process. Generated power is useless if it is not efficiently transferred to the application.
Over 90% of all applications in the field use glass (reactors, distillation apparatus, etc.), and the maximum allowable system pressure for these applications is 0.5 bar. Circulation pumps are ideally designed so that turbulent flow generates a large heat transfer coefficient (alpha value) and thus efficient heat transfer at the internal heat exchangers (evaporator and heater). Unistat pumps therefore prefer to generate circulating flow instead of circulating pressure and usually require significantly lower (pump) motor power to do so.
The installation and design of the overall system is often considered almost secondary. Here, too, there are numerous aspects that have a direct influence on the temperature control performance. One important aspect is, of course, the selection of a suitable thermal fluid. In addition, the quality and condition of the temperature control hoses have a direct effect on the achievable performance. Metal temperature control hoses with a smooth inner wall are therefore available for Unistats. These hoses improve the flow behavior and thus the heat transfer - resulting in significant time savings during heating and cooling. Other points with a negative effect are crushed hose connections, unnecessarily long connection paths or a small cross-section of the hoses or hose adapters.
Case studies are often helpful as a source of information for purchasing decisions. Case studies document heating and cooling processes and show typical scenarios such as the control behavior during an exotherm. Case studies enable a reliable prediction as to whether the temperature control unit is suitable for the intended application.
There are several points to consider when selecting a thermostat. Ultimately, not only the heating and cooling capacities specified in the manufacturer's catalog are relevant rather, criteria such as cooling capacity density, flow rate and, if applicable, case studies should be in the foreground, as this is the only way to make a practical assessment of heat transfer efficiency.
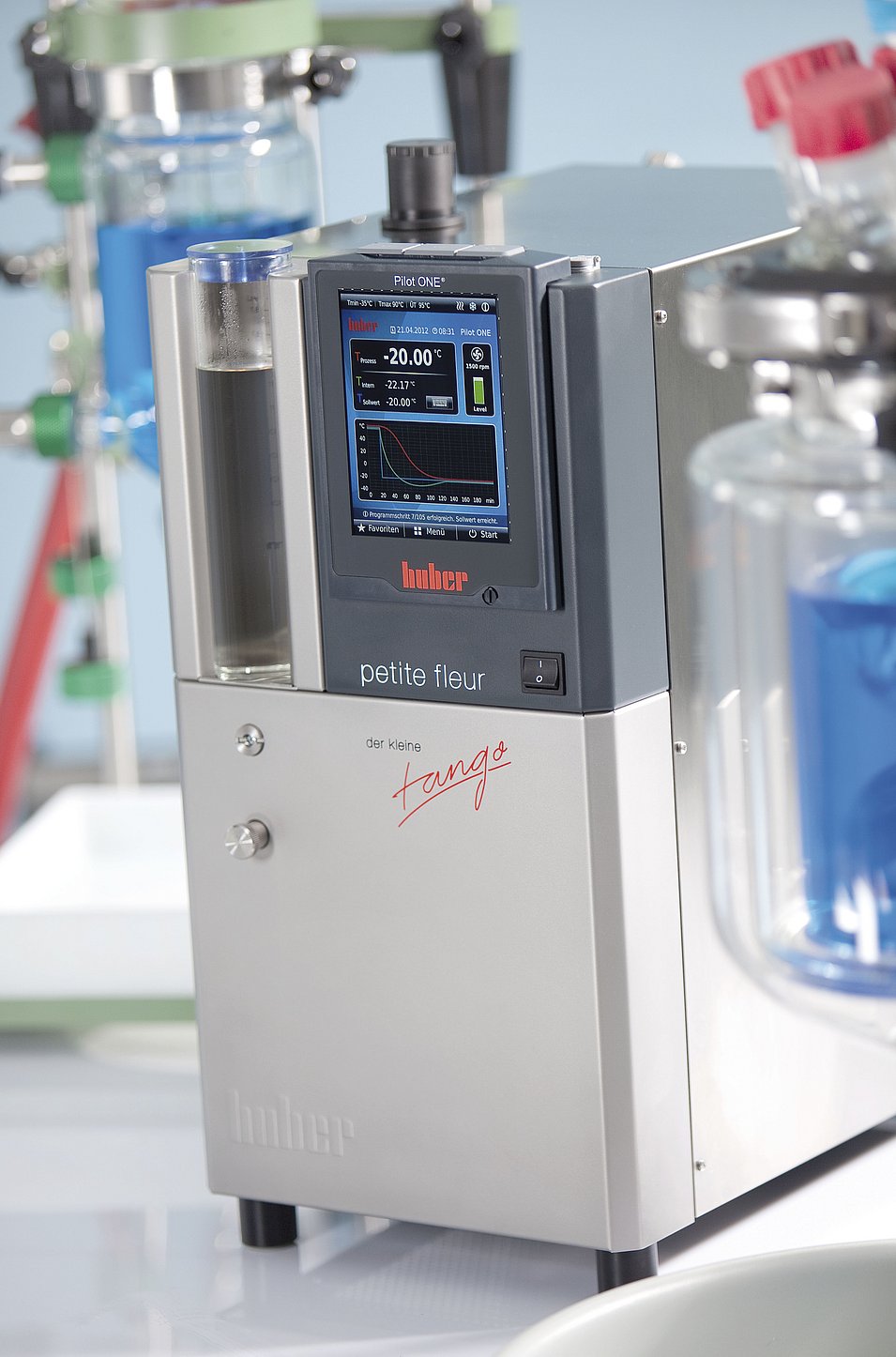
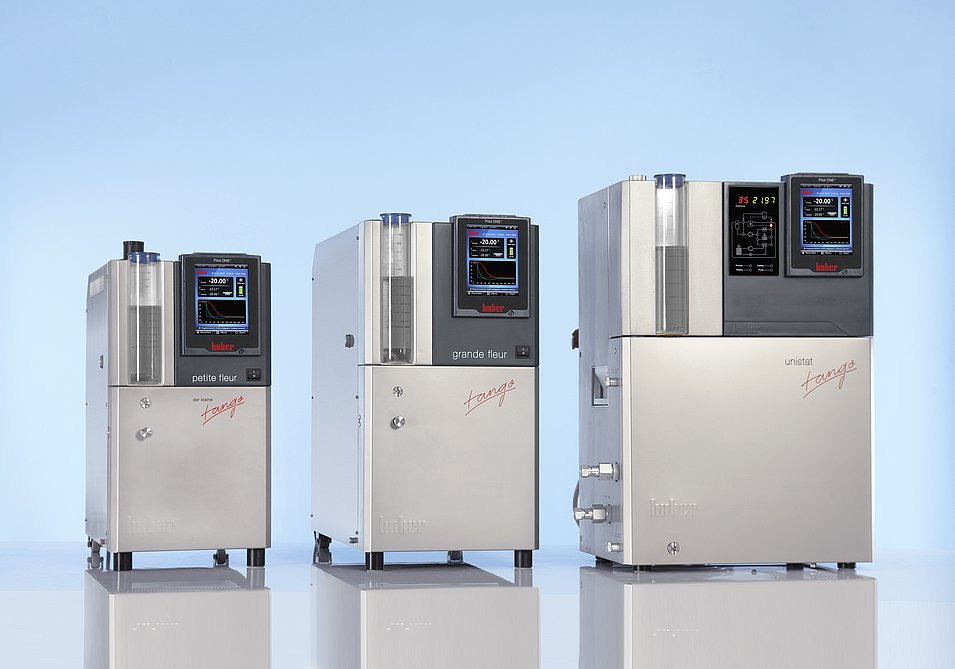